Getting your Trinity Audio player ready...
|
A Ghanaian lawmaker has sued the government for sole sourcing a $12 million medical deliveries through drones with Fly Zipline Ghana Limited.
Opposition MP Ernest Norgbey contends per the Public Procurement Act, there was no justification for the government to sole-source the contract to Fly Zipline.
The Ashaiman legislator is seeking a declaration that “the Government of Ghana erred in using single sourcing method of procurement in engaging Fly Zipline Ghana Ltd for the implementation of Zipline RPAS for the delivery of blood products.”
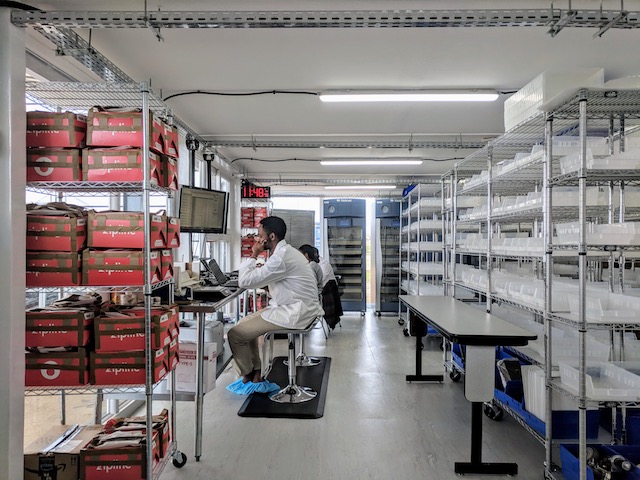
He also wants a declaration that the service agreement was “illegal and therefore void” and an order “invalidating the service agreement.”
The National Democratic Congress legislator argues that other options were not assessed before the government settled on Fly Zipline for the implementation of the project.
He further argues in the writ that the government “did not do due diligence or survey the market before embarking on single sourcing method of procurement.”
The MP maintains further that “the government has an obligation to do due diligence and survey the market to ascertain that a company [Fly Zipline] is the only supplier or service provider before using the single sourcing method of procurement.”
Zipline’s Safety System
Zipline’s drone delivery service is dedicated to expanding healthcare access and saving lives around the globe. Health workers place orders by text message and receive their deliveries in 30 minutes on average. Zipline’s drones both take off and land from its distribution centers, requiring no additional infrastructure at the clinics it serves. Deliveries are made from the sky, with the drone descending to a safe height above the ground and air-dropping medicine by parachute to a designated spot at the health centers it serves.
Because the company’s drones criss-cross commercial airspace daily over both remote and populated areas on their way to deliver critical and lifesaving medicine to people in need, the safety and reliability of Zipline’s service is a top priority. Recently, the United States Federal Aviation Administration announced that it may require the U.S. commercial drone industry in future regulation to adopt the kinds of safety features Zipline has already put in place. The company has taken many steps to ensure that it is operating the safest delivery system of its kind in the world including rigorous testing of flight software and aircraft hardware; flight operations safety procedures; redundant inflight safety features; and modular frangible design.
Rigorous Testing of Flight Software and Aircraft Hardware
The company works to improve the quality of its code and service every day to make sure it is operating the safest and most effective drone delivery operation in the world. All software updates are first put through automated software and hardware in the loop testing. Allowing advanced algorithms to assess how the new code and aircraft would perform in the real world.
After passing through simulation testing, all new code is installed onto drones at our state of the art flight testing facility in Northern California, Codenamed Nest X, and pushed to the limits to validate performance. That process is repeated until the system and aircraft are ready to be deployed into global flight operations.
Flight Operation and Safety
Flight operators physically inspect each aircraft and use cutting edge technology like computer vision during preflight checks to make sure each drone is fit for flight. Because Zipline’s drones fly autonomously along predetermined routes, all of our flight paths are registered in advance with civil aviation authorities.
Zipline is in direct communication with those aviation authorities so that they know at all times when drones launch and where they are flying. Zipline’s sophisticated air traffic control system uses advanced algorithms to make sure all drones in the air know where they are, where they need to go.
Redundant In-flight Safety Features
Zipline drones are designed to automatically detect issues inflight and safely
return to base for repair. Each drone is equipped with redundant flight computers, motors, communications systems, flight control surfaces, as well as redundant navigation and power systems.
In the event of emergencies like severe weather, emergency requests from air traffic control or unplanned flight operation issues, each drone is equipped with a parachute that allows it to make an immediate landing by slowly descending to the ground.
The drones use parachute landings at least once a week during the the testing and diagnostic phase of beginning new distribution centers and delivery routes or when the company decides to make deliveries in the face of extreme weather to aid in emergency medical situations.
Modular Frangible Design
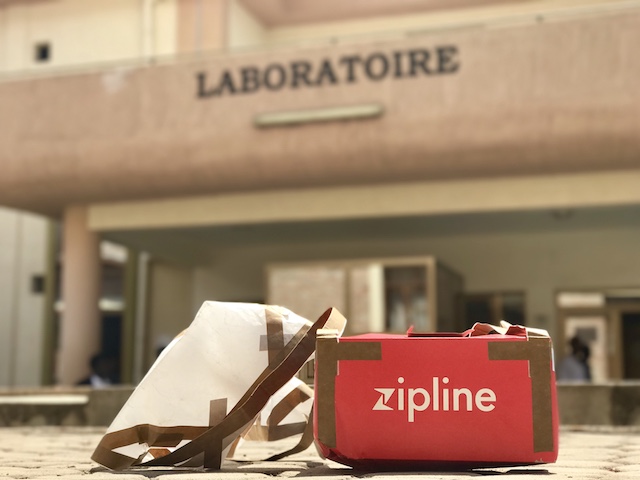
Zipline’s drones and its parts are designed to break on contact minimizing potential damage to things on the ground. The drone’s core navigation, power, communications, and computing functions are inserted into the drone as a single unit. That unit is housed within a carbon fiber chassis that is protected by an outer styrofoam shell, similar to construction of helmets. The styrofoam serves to protect anything on the outside of the drone as well as everything on the inside.
Damaged styrofoam is quickly replaced allowing the drone to return to service. The same is true for other flight modules, which include the motors, wings, tail fins and power, navigation and communications unit. If any one of those units experiences issues, it can be easily replaced with a new one so that the aircraft can return to service saving lives as quickly as possible.
Source: Daily Mail GH